- +54 9 11 4433-3338
- info@tpi.ar
- Juan Jose Paso 56 5°E, Martinez, Bs As, Argentina
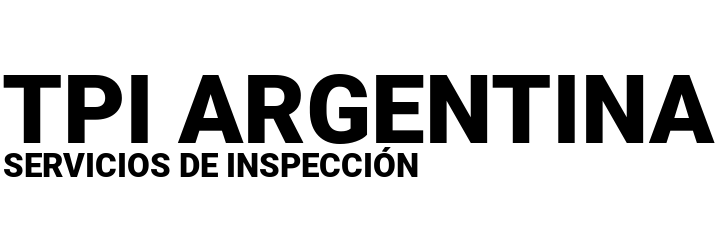
Auditoría de Fábrica
WHAT IS A FACTORY AUDIT?
A factory audit is a systematic process designed to assess whether a production facility meets specific standards in key areas such as quality, safety, legal compliance, operational capabilities and sustainability. Its purpose is to identify strengths, weaknesses and risks, ensuring that factory processes and practices are aligned with customer requirements and applicable regulations.
ADVANTAGES OF PERFORMING A FACTORY AUDIT BEFORE OPERATING WITH A NEW SUPPLIER:
– Avoid undesirable and unexpected surprises: Allows hidden problems to be detected before making a commitment.
– Do not assume that the supplier will meet the requirements: Ensures that the factory has the real capacity to satisfy the order.
– Prevent delivery delays: Identifies possible limitations in production or logistics times.
– Avoid overruns: Reduces the risk of additional expenses due to non-compliance or subsequent rectifications.
– Guarantee product quality: Helps to avoid receiving non-conforming products that may cause future problems.
– Prevent claims from the end customer: Ensures that the delivered products meet the required expectations and standards.
WHAT IS A FACTORY AUDIT FOR?:
– Confirm the existence of the company and its physical location.
– Verify permits and authorizations: Ensure that it operates legally.
– Evaluate quality management processes: Identify the level of standardization and implementation.
– Review available stock: Ensure that it can meet orders.
– Analyze tools and equipment: Confirm that it has the necessary resources for production.
– Examine the condition of the equipment: Determine if it is modern or needs replacement.
– Evaluate facilities and working conditions: Verify the safety and well-being of employees.
– Review claims and stock management: Evaluate efficiency and organization.
– Measure the capacity and flexibility of processes: See if it can meet specific customer requirements, such as customization, quantities, delivery times, packaging and documentation.
– Evaluate readiness to change : Know if the supplier can adjust its processes to meet customer expectations.
– Get a first impression of new suppliers: Determine their reliability and compliance capacity.
In short, auditing is a key tool to assess whether a supplier is capable, reliable and suitable to meet customer expectations.
Newsletter
¡No te pierdas nuestras futuras actualizaciones! ¡Suscríbete hoy!
©2023. TPI Argentina. Todos los derechos reservados
- +54 9 11 4433-3338
- info@tpi.ar
- Juan Jose Paso 56 5°E, Martinez, Bs As, Argentina